Industrial Thermal Imaging
Pre-emptive maintenance solutions.
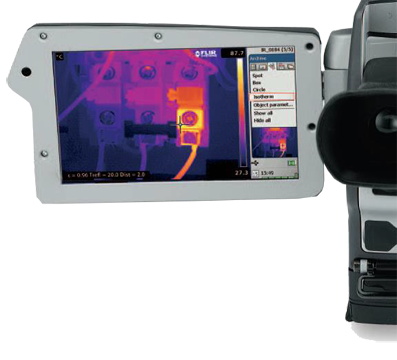
Industrial Thermal Imaging
Electrical & Mechanical Equipment get hot before it breaks down. See it before it happens – a stitch in time…
“35% of all industrial fires are created by electrical problems”. Schedule your shutdown around production timetables before a catastrophic failure happens.
We provide thermal imaging reports to senior management or insurance companies of potential problems with electrical and mechanical equipment before it happens.
Why choose us?
Our Flir P620 high definition thermal imaging camera has a 640 x 480 detector, which delivers 307,200 pixels versus 16 times better than a thermal imaging camera with a 160 x 120 detector! We use this camera in the utility industry because it can see greater detail with smaller targets while still looking at the larger picture. This is important because it improves worker safety. This type of thermal imager can be used on large machinery, production lines, electrical switch rooms, substations, switchyards, transmission and distribution lines.
We provide top- level detailed, sharp- looking thermal imaging photos and informative reports to senior management or insurance companies of potential problems with electrical and mechanical equipment before it happens.
Why Infra Red?
Light at frequencies bellow red is called infrared. The human eye cannot see it, but infrared detectors and imaging devices can. All objects emit infrared energy at ordinary temperatures. The hotter the object, the more infrared energy it emits. We use infrared cameras to detect and measure an object’s emitted energy.
Since nearly everything gets hot before it fails, a non- contact thermal imaging survey makes an extremely cost-effective and valuable diagnostic tool – Maintenance Technology Magazine reported a €4 return on every €1 spent on infrared inspection
You can see the problem before it happens so you can now schedule your shutdown around production timetables before a catastrophic failure happens.
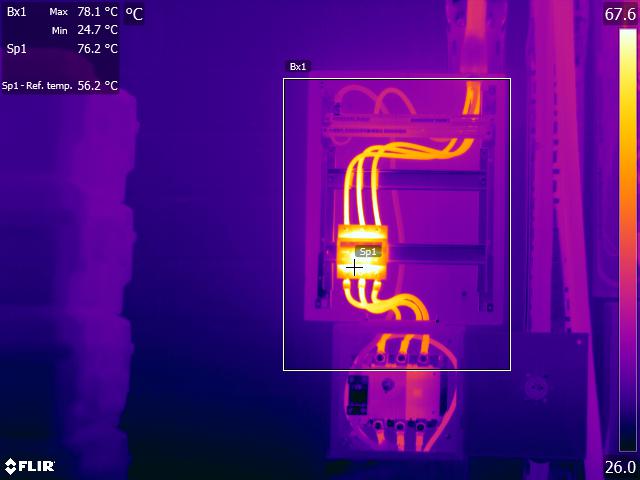
This cable is 75° C, urgent attention is required as the cable is twice it’s design temperature.
Electrical Systems
Thermographic inspections are commonly used for electrical installations. Any resistance to electrical current causes an increase in temperature. This increased temperature can then cause components to fail, potentially resulting in unplanned outages and injuries. If left unchecked, heat can rise to a point that connections melt and break the circuit. This can result in fire, 35% of all industrial fires are created by electrical problems resulting in losses of 300 Billion euros per year.
Besides loose connections, electrical systems suffer from load imbalances, corrosion and increases in impedance to current. Thermography can quickly locate these hot spots, determine the severity of the problem, and help establish the time frame in which the equipment should be repaired. It is very useful when inspecting indoor components such as motor control centres, breaker panels, disconnect switches, and transformers. Additionally, outdoor components, substations, switchgear, transformers and outdoor circuit breakers can be inspected quickly.
Mechanical Systems
In many industries, mechanical systems serve as the backbone of operations. Typically, when mechanical components become worn and less efficient, the heat dissipated will increase. Most mechanical systems will also heat up if there is improper lubrication or misalignment. Consequently, the temperature of faulty equipment or systems will increase rapidly before failure.
Typical mechanical systems monitored in a predictive maintenance infrared program include bearings, motors pumps, compressors and conveyer systems.
Thermographic data can be an invaluable source of complimentary information to vibration studies in this area of equipment monitoring. Electric motors can be observed for brush –contact and armature shorts, both of which typically produce excess heat prior to failure but remain undetected with vibration analysis. Suspected roller – Overheated windings in a motor, overheated bearings.